Maintenance Strategy at its Core
Since maintenance affects all pieces of equipment, companies should build or at least be aware of their upkeep strategy. But what exactly is maintenance? The phrase refers to the actions taken to keep equipment, machinery, buildings, or systems in optimal working condition and prevent unexpected failures, thereby managing maintenance costs effectively. This can include routine inspections, repairs, and servicing.
The maturity of the maintenance strategy depends on many different factors such as costs, criticality, or environment. There are different approaches to building such strategies within a company. See some examples on the diagram below.
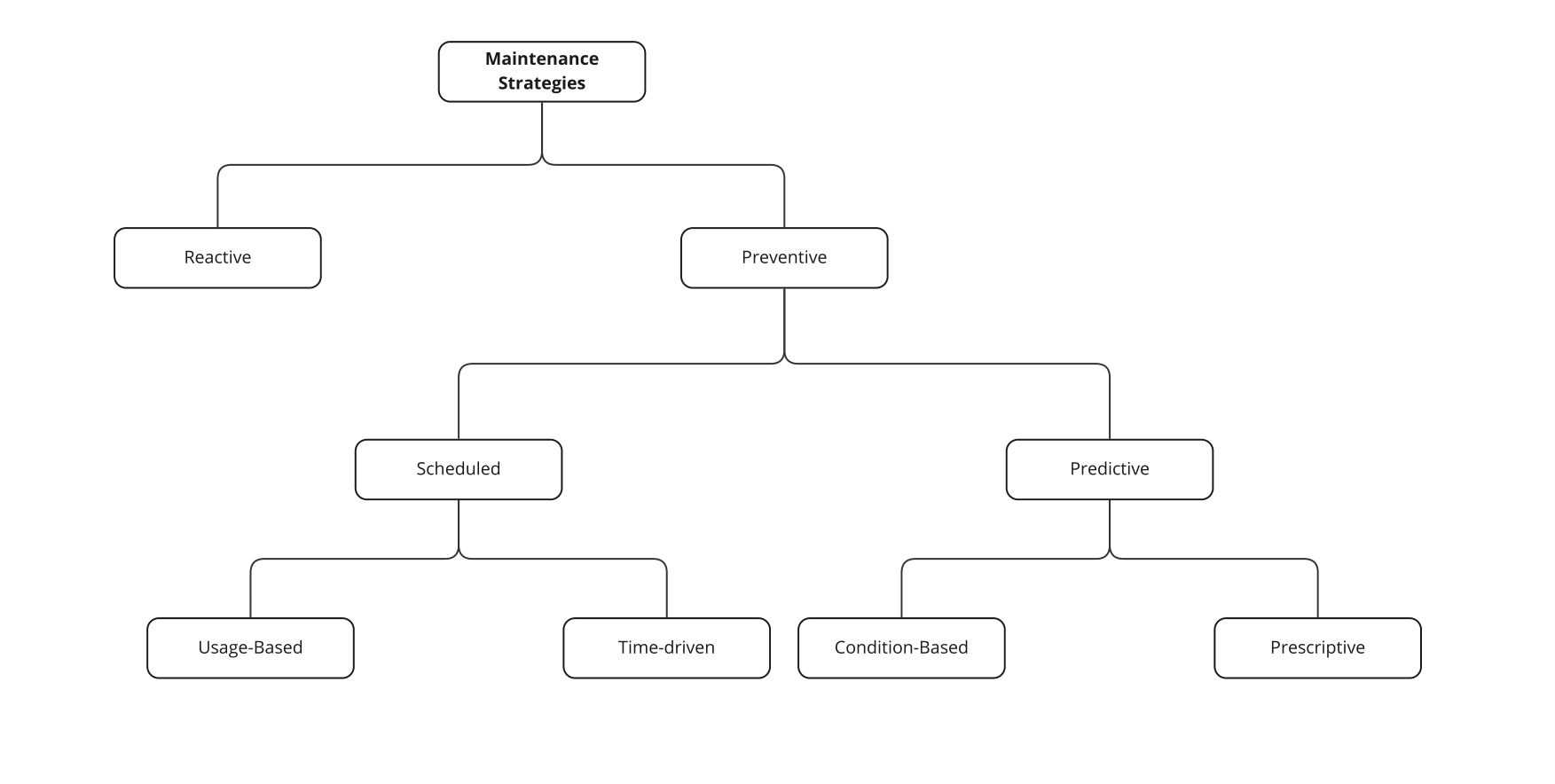
Reactive Maintenance
The simplest maintenance strategy assumes repair once a piece of equipment is broken. The goal of this strategy is to fix the failure when it occurs. This approach is characterized by a long period of downtime when the equipment is out of use until the fix is applied. Depending on the equipment and business area this may lead to significant costs to the company.
For example, in a manufacturing plant, if a conveyor belt suddenly malfunctions, reactive maintenance would be employed to quickly diagnose and repair the issue to minimize downtime. This approach is crucial in scenarios where unplanned equipment failures could severely affect production schedules and operational efficiency.
Preventive Maintenance
In opposition to reactive maintenance, there is a group of strategies where we aim to prevent the failure of the device by for example conducting regular, predefined maintenance in a restricted schedule or by conducting more sophisticated failure predictions. This proactive approach minimizes equipment downtime and blocks excessive loss in production through effective maintenance scheduling.
For instance, in an office building, routine inspection and servicing of HVAC systems can prevent sudden breakdowns and ensure a consistent, comfortable environment for employees. This approach helps extend the lifespan of equipment and reduce the likelihood of costly emergency repairs.
Scheduled Maintenance
The simplest preventive strategy is scheduled maintenance, which involves routine maintenance tasks performed at regular intervals. However, in this case, a maintenance window that occurs every scheduled period impacts the production. Thus, the total cost related to this strategy may be lower compared to the reactive strategy yet, the cost of upkeep for very specialized equipment may be significant and may impact the budget.
Moreover, this approach seems to be inaccurate and inflexible due to the fact that it is based on the developed algorithms of how to conduct regular maintenance instead of the current status and health of the device.
Picture this: In a fleet management company, vehicles receive oil changes, tire rotations, and brake inspections every 5,000 miles. This routine maintenance helps prevent unexpected breakdowns and keeps the fleet operating efficiently. However, this strategy doesn’t count for every driving style. If you’re an extremely calm driver, you may not overuse the breaks or test engine and the tires too much. Compare it with someone who likes a more dynamic way of driving which puts more impact on these parts, and there’ll be a difference.
Predictive Maintenance
Another preventive approach is called the predictive maintenance strategy. It optimizes the costs of handling regular upkeep through a prediction of when maintenance is exactly needed. Implementing predictive maintenance can significantly reduce equipment downtime and operational costs. On the other hand, it avoids situations when the equipment reaches a state of failure.
A bitter pill to swallow here is that despite its obvious benefits a predictive maintenance strategy may only be implemented in a situation where there is data collected that can be used in further analysis. Other challenges very often relate to the integration aspect and concerns regarding data privacy. A predictive maintenance program provides real-time analytics of critical assets, optimizing maintenance scheduling based on actual equipment usage.
Sometimes the predictive maintenance strategy is also called Data-Driven Maintenance to emphasize the impact of the data in the entire approach. Depending on the data that is collected for the equipment, a predictive maintenance strategy can be built on different levels which makes this approach even more effective. Predictive maintenance software enhances operational efficiency by monitoring machinery conditions and anticipating failures before they occur.
In a commercial airline operation, predictive maintenance uses data from onboard sensors to continuously monitor engine performance and wear. By analyzing this data, the maintenance team can predict when specific engine components are likely to require servicing or replacement, scheduling maintenance during planned ground time rather than dealing with in-flight issues or unexpected groundings. This ensures higher reliability and safety while optimizing maintenance schedules and reducing operational disruptions. Vibration analysis is a key technique in predictive maintenance, allowing for timely interventions by monitoring changes in vibration patterns.
Condition-Based Maintenance
On the highest level of predictive maintenance, predictive maintenance solutions aim to detect the state and predict the time when upkeep should be performed to avoid failure. This approach is related to the overall health of the equipment and predicts whether the equipment as a whole requires maintenance.
For example, in a mining operation, the hydraulic systems of heavy machinery are equipped with sensors that monitor parameters like oil viscosity and particulate levels. Maintenance is then performed only when the output of the analysis shows that the maintenance window should happen soon as the condition of the machine is showing signs of degradation, ensuring that equipment is serviced exactly when needed, enhancing reliability, and reducing unnecessary costs.
Prescriptive Maintenance
Thanks to Big Data and the Internet of Things (IoT), the data we collect is getting more and more detailed, sometimes connected with hundreds of small sensors of equipment, making predictive maintenance work more precise. This fact leads to another, more detailed predictive maintenance strategy called prescriptive maintenance where the goal is to predict the failure of a particular piece of equipment. This gives information not only about a potential failure but also about what part is going to break down.
Such an approach is extremely useful when utilized in sophisticated equipment and the maintenance can be precise and dedicated to a small area. This leads even further to cost optimization.
A used case is a chemical processing plant, where advanced analytics might not only identify that a pump is likely to fail within two weeks due to increasing vibration levels but also prescribe specific actions, such as replacing a worn bearing and adjusting operating conditions to prevent rapid wear. This approach optimizes maintenance activities by offering precise, data-driven guidance, thereby enhancing both equipment reliability and overall operational efficiency.
Optimize Your Business with Predictive Maintenance
The evidence of effectiveness that comes from the implementation of Artificial Intelligence algorithms into the maintenance area is becoming more visible and documented in research papers and real case studies from different industries. With advanced AI techniques and the ability to analyze bigger datasets, the benefits are more emphasized and tangible. A big step in predictive maintenance was achieved by leveraging deep learning techniques that led to improved prediction accuracy and the capability to handle huge amounts of data to analyze.
Predictive maintenance programs can lead to substantial annual savings and efficiency improvements for facilities.
Another important improvement comes from chaining different techniques and approaches in the overall process of upkeep. This leads to better process coverage and relying on multiple distributed algorithms working together instead of just one.
Save Costs with Predictive Maintenance
Implementation of predictive maintenance may lead to several business benefits with maintenance costs savings as the leading one. The ultimate goal of predictive maintenance is to eliminate costly repairs and recurrent costs of scheduled maintenance.
Predictive maintenance aims to optimize the cost of upkeep by providing relevant information just in time to make maintenance windows very specific and precise. Moreover, predictive maintenance leads to an improvement in resource utilization by minimizing the need for routine scheduling.
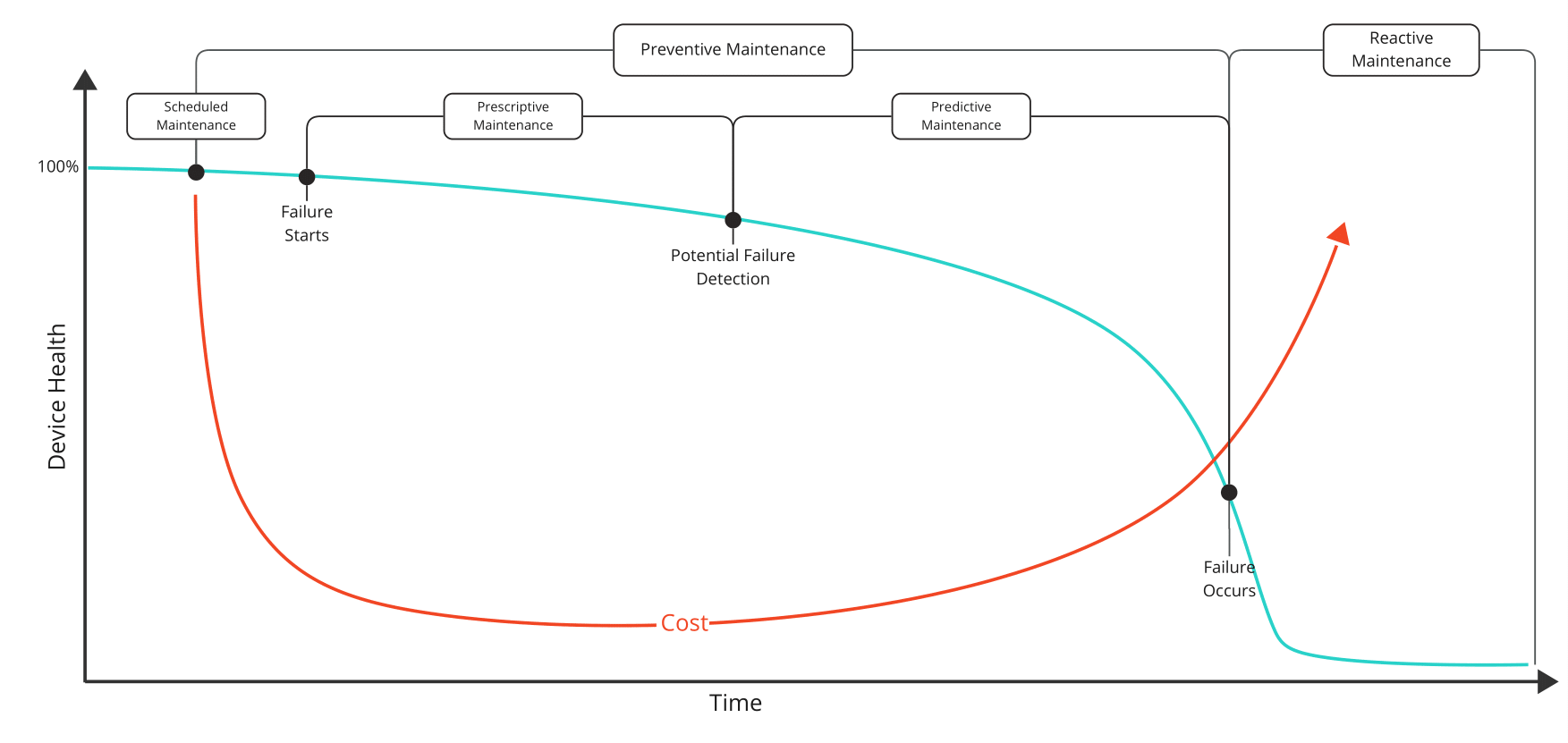
Extend Your Equipment’s Life
Another interesting benefit of applying the predictive maintenance strategy is the extended life of the equipment that is under control. Through dedicated maintenance companies can achieve a state where the cost of maintenance is minimized to only required pieces of the device.
By assessing the health of the device it is possible to plan the maintenance accordingly and extend the lifetime of its parts to avoid regular and time-based scheduled replacements of unused parts. This approach is mostly visible in the prescriptive maintenance area.
Be Assured of Your Safety
By minimizing the failure occurrence, the predictive maintenance approach can significantly increase the safety of people involved in the process as well as the overall business. Avoiding unexpected and expensive fixes the overall business remains more stable and predictive and less prone to any downtime. Moreover, unexpected failures may lead to more severe situations endangering the health and safety of people involved in the process.
Operate on Your Highest Efficiency
Another crucial benefit that comes from the predictive maintenance approach is increasing operational efficiency by minimizing unplanned downtime. By achieving a stable and predictable production process with minimized risk of downtimes, operational efficiency can increase significantly and allow the company to plan the workload and supply and fulfill contractual obligations.
Transform your Maintenance
Maintenance is everything. Make sure your updates are up to the minute, all functions are operating at their highest efficiency, everything is intact and ready to make your business grow and expand. Cost saving and minimizing downtime support not only the company and their employees, but also the clients – portraying the business as reliable, modern and resilient, ultimately safe to work with.