Enhancing Efficiency with Predictive Maintenance Programs
Picture a wind farm operator getting an advance notice about a potential turbine issue. Such a proactive approach is made possible by predictive maintenance. Using AI algorithms, operators can foresee equipment issues before they arise, transitioning maintenance from a reactive to a proactive endeavor. Implementing predictive maintenance can lead to substantial cost savings and increased equipment reliability, though it requires significant investment and careful planning to integrate with management systems. This approach drastically reduces unplanned downtime and extends the lifespan of assets.
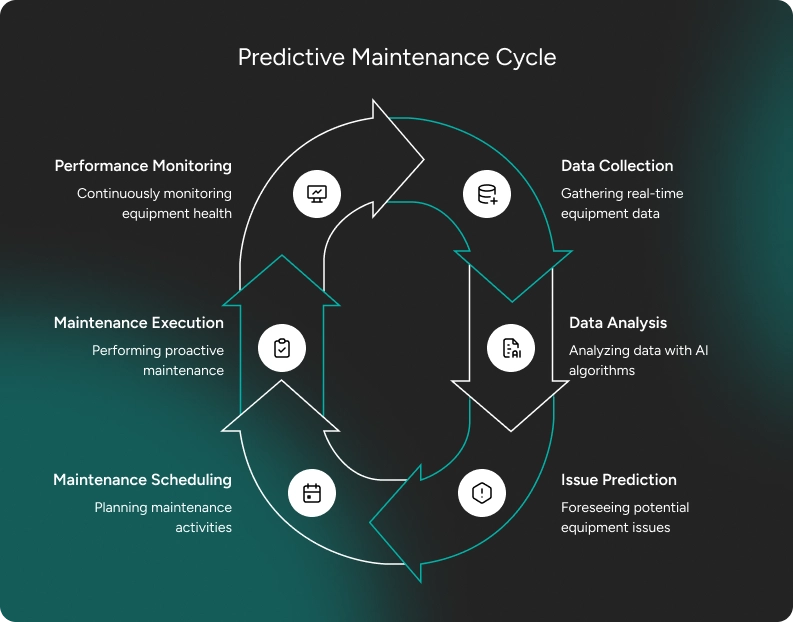
For instance, a company in the wind energy sector integrated AI-driven predictive maintenance to monitor turbine vibration, temperature, and historical performance data. This foresight allowed them to schedule maintenance during off-peak hours, reducing disruptions and ensuring continuous energy supply. Effective maintenance scheduling, based on real-time data and equipment condition, is essential for minimizing downtime and costs. The result? A significant reduction in maintenance costs and an impressive increase in turbine lifespan.
The maintenance team plays a crucial role in this process by monitoring equipment health and scheduling proactive maintenance based on predictive models, leveraging centralized data to improve operational efficiency and reduce downtime.
Precision Planning Through Quantitative Models
Quantitative modeling provides a strategic edge, enabling companies to simulate operating conditions and explore various maintenance scenarios. This approach helps energy companies make well-informed decisions, optimize maintenance schedules, and allocate resources efficiently. Predictive maintenance programs play a crucial role in optimizing asset reliability by preventing unexpected equipment failures and enhancing operational efficiency.
Take a power plant, for example. By utilizing quantitative models, they could simulate wear and tear on their turbines to predict when and where components might fail. This allowed them to adjust their maintenance schedules proactively, resulting in minimized wear, extended equipment lifespan, and substantial cost savings. Predictive maintenance helps avoid unnecessary maintenance costs by performing maintenance only when required, based on real-time data, thus preventing excessive expenditures. Such precision planning not only boosts efficiency but also fortifies the reliability of their infrastructure.
Tailored Solutions with Custom Software Development
What good is data if it’s not actionable? This is where STX Next’s custom software solutions come into play. We translate insights from AI and quantitative models into intuitive, user-friendly tools. These solutions integrate data, apply AI models, and offer actionable insights through easily navigable dashboards and reports, empowering maintenance teams to make swift, data-driven decisions. Predictive maintenance software plays a crucial role in monitoring equipment health and preventing potential failures by utilizing predictive analytics to alert maintenance teams about equipment stressors.
Imagine a real-time dashboard tailored for energy companies. It provides alerts on predictive maintenance, displays equipment health status, and tracks historical performance trends. Such a dashboard ensures maintenance teams can prioritize tasks effectively, reducing response times and enhancing operational efficiency. Integrating predictive maintenance data into a computerized maintenance management system as part of a predictive maintenance solution enhances equipment reliability and reduces downtime costs.
Insights from the Field
I recently attended the "The Connected Worker Chicago Exchange" conference in Chicago, which brought together technology and business leaders from leading energy and manufacturing companies across the U.S. The discussions, debates and shared insights at this event highlighted the critical need for advanced technologies like AI and GenAI to improve safety, efficiency, productivity, and business outcomes. This experience reinforced my belief in the transformative power of these technologies in the energy sector.
Driving Business Benefits
Combining AI, quantitative modeling, and custom software development transforms energy maintenance into a streamlined, efficient process. These technologies culminate in higher efficiency, reduced operational costs, and enhanced safety standards. Predictive maintenance work combines monitoring and analysis of equipment conditions using advanced technologies such as IoT and machine learning. Predictive maintenance reduces downtime, quantitative modeling fine-tunes planning, and custom software operationalizes insights seamlessly.
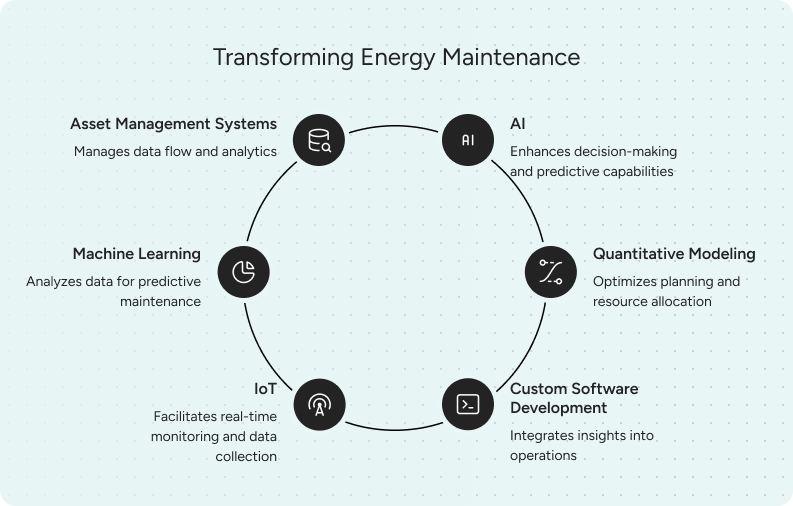
Asset management systems facilitate data flow and analytics for improved decision-making, ensuring that maintenance managers and teams can monitor equipment failure and maintenance tasks effectively.
Energize Your Business with STX Next
The future of energy management is here, and it’s powered by advanced technologies that predict, prevent, and perform. At STX Next, we pride ourselves on being more than just a service provider; we are a partner in your success. Our deep technological expertise and tailored solutions are designed to elevate your maintenance strategies.