What is RAG and Large Language Models?
Retrieval Augmented Generation (RAG) is like a super-efficient assistant who can instantly pull up all the maintenance records, manuals, and past issues of every machine under your care. Then, it uses all that information, along with external knowledge, to tell you which machine might need servicing soon or what part you should order before it breaks down. It can even create diagnostic instructions for a defect that has never been previously documented.
This makes it ideal for applications where information is highly complex and in different forms.
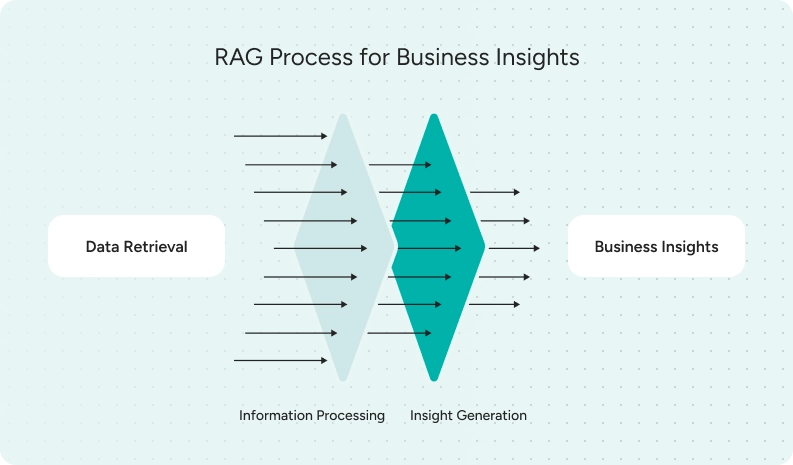
Practical Magic of RAG: Streamlining Manufacturing with Informed Decisions
Enhancing Quality Control with Data-Driven Insights
Quality control is often comparing previous control values with current values. RAG systems can do this in real time on a massive scale. RAG can assist in detecting anomalies by using relevant information from databases and predicting potential defects before products leave the factory floor, ensuring consistently high quality and reducing waste.
Predictive Maintenance Made Perfect with RAG and Predictive Maintenance
For the last few years, the most advanced predictive maintenance detection systems have been based on earlier-generation AI (Artificial Intelligence). One of the benefits of Retrieval Augmented Generation is that an even more powerful AI is applied to all of your systems– new and old. This of course means less downtime, lower maintenance costs, and an overall boost in productivity.
Elevating Safety Standards with Informed Risk Assessment
Safety is a top priority in manufacturing, and the advent of Retrieval Augmented Generation enhances the ability to assess risks with unprecedented precision. Traditional systems can often provide outdated or inaccurate responses due to their reliance on pre-trained knowledge, but RAG mitigates this by accessing external information sources for more accurate and current answers.
By sifting through safety reports, incident logs, and compliance guidelines, RAG can alert management to areas of concern and help develop more effective safety protocols, minimizing the likelihood of accidents. “You can ask a RAG system why is safety protocol A better than our existing protocol B and cite your evidence.”
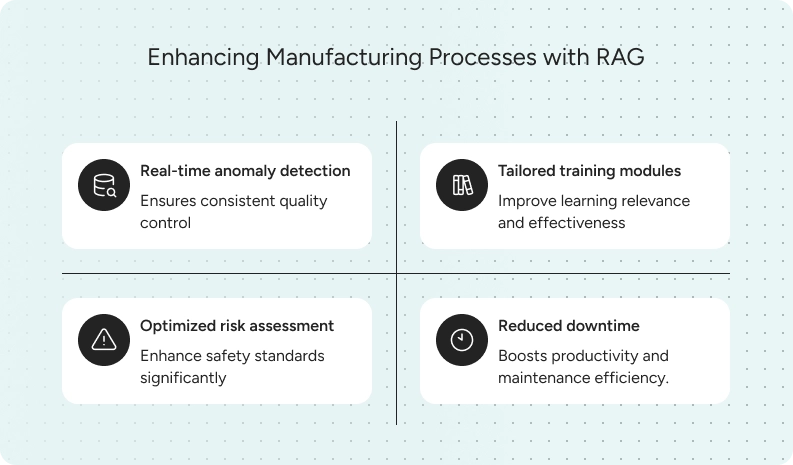
Enabling Customized Training through Knowledge Retrieval
Training manufacturing personnel can often be time-consuming and generic. RAG provides a solution by customizing training materials based on job roles, current trends, and individual learning progress, utilizing training data to ensure relevance and effectiveness. This means great training even when the budgets are cut.
RAG in Action: Case Studies of Success
Understanding the theoretical benefits of Retrieval Augmented Generation is one thing, but seeing it in practice truly solidifies its value. Real-world applications of RAG provide compelling evidence of its value in manufacturing. Here are three examples where RAG’s impact was measured:
Aerospace Component Manufacturer Reduces Inspection Time
An aerospace manufacturing company integrated a RAG system to enhance its inspection process. By retrieving and synthesizing past inspection reports, specifications, and standards, the RAG tool was able to guide inspectors through complex quality checks. By efficiently retrieving relevant documents, the system ensured inspectors had all necessary information at their fingertips. The result was a 40% reduction in inspection times and a notable improvement in defect detection rates.
Automotive Factory Achieves Predictive Maintenance Mastery
A prominent automotive manufacturing plant employed a RAG solution to anticipate maintenance needs for their assembly line robots. The system analyzed real-time operational data along with years of maintenance logs to predict failures before they occurred. The downtime was minimized, and the plant saw an annual maintenance cost reduction of 25%.
Chemical Producer Elevates Safety with Dynamic Risk Assessment
A chemical producer used a RAG-powered platform to revamp its safety protocols. By processing incident reports and material safety data sheets, the platform identified previously unnoticed patterns of safety risks. Implementing the new safety measures informed by RAG insights led to a 30% decrease in safety incidents over the course of a year.
Shaping the Future of Manufacturing
Retrieval Augmented Generation is not a distant, futuristic concept – it is a here-and-now solution with tangible benefits to the manufacturing industry. By introducing RAG into your operations, you’re not just adapting to the evolving landscape of Industry 4.0; you’re actively shaping it.
Implementing RAG can significantly reduce computational and financial costs, making it a cost-effective solution for manufacturing enterprises. From superior quality control to predictive maintenance and enhanced safety protocols, RAG stands to redefine the capabilities of manufacturing professionals across the board.
Lastly, the deployment of RAG is not a classic rip-and-replace IT technology product. Instead, it layers on top of everything that already exists and starts working on all the use cases immediately.