What Is Predictive Maintenance?
Predictive maintenance (PdM) helps businesses spot equipment failures before they happen. It uses real-time data from sensors, paired with machine learning algorithms and predictive analytics, to identify patterns and predict when a failure might occur.
For example, condition monitoring tools like vibration analysis can alert teams to unusual patterns that indicate wear or damage. Predictive maintenance software collects this real-time data and analyzes it, giving maintenance personnel a chance to fix problems early.
This proactive approach means fewer breakdowns, smoother operations, and longer machine life. It also improves scheduling by only performing maintenance when needed – minimizing costs and freeing up resources.
Challenges of Predictive Maintenance
While predictive maintenance strategies have clear benefits, they also come with challenges. The system relies on high-quality, accurate data. Poor or incomplete data can lead to false alerts – or worse, missed problems.
There’s also an upfront cost. Organizations need to invest in IoT sensors, predictive maintenance solutions, and the infrastructure to support them. On top of that, teams need to know how to interpret the data, so training is a must.
Real Example: Monitoring Motors in Manufacturing
A manufacturing plant used predictive maintenance to track the health of dozens of motors. By installing sensors and using vibration analysis, the company could detect early signs of potential failures. The system flagged motors that were at risk, and maintenance teams fixed the issues before breakdowns happened.
The result? A 30% reduction in unplanned downtime and a noticeable boost in productivity.
What Is Prescriptive Maintenance?
Prescriptive maintenance (RxM) builds on predictive maintenance by not only predicting equipment failures but also suggesting what to do next. It uses artificial intelligence and machine learning to analyze data and generate specific, actionable recommendations.
In short, prescriptive maintenance systems tell you not just what might go wrong – but why it might happen, how to fix it, and when to act.
This makes preventive maintenance even more effective. Maintenance teams can pinpoint the root cause of issues and take targeted action, whether that’s adjusting machine settings, ordering spare parts, or scheduling repairs at the ideal time.
Benefits of Prescriptive Maintenance
- Detailed root cause analysis
- Optimized maintenance activities
- Better decision-making support
- Fewer safety incidents and more equipment uptime
These systems support broader operational goals, improving equipment reliability and maximizing the value of every maintenance dollar spent.
Challenges of Prescriptive Maintenance
Prescriptive maintenance requires more advanced technologies, deeper data analysis, and often, more investment. Businesses must build or buy the infrastructure to support prescriptive analytics and train staff to use it.
However, the payoffs – especially for organizations dealing with critical equipment – can be significant.
Real Example: Aircraft Fleet Management
An airline implemented a prescriptive maintenance program across its fleet. Sensors collected real-time data from aircraft engines and systems. The prescriptive analytics engine predicted potential failures and recommended exact steps to prevent them.
For instance, it flagged a recurring issue with an avionics system and suggested replacing a particular part before it failed. This cut unscheduled maintenance by 20%, reduced delays, and lowered operational costs.
Predictive vs. Prescriptive Maintenance: Key Differences
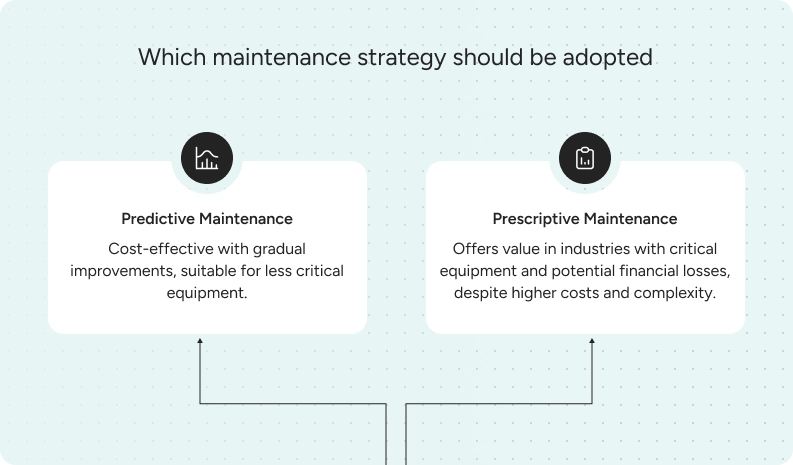
Both predictive and prescriptive maintenance aim to prevent equipment failures and reduce downtime. However, they differ in how far they go:
- Predictive maintenance focuses on identifying when a failure might occur.
- Prescriptive maintenance offers recommendations on what to do to prevent it.
Prescriptive maintenance takes predictive insights further by recommending specific, data-backed actions. This makes it more complex – but also more powerful.
Key Considerations When Choosing
If you're weighing predictive vs. prescriptive maintenance, ask yourself:
- Industry Needs: Are you in a high-stakes industry like power plants or aviation? Equipment downtime or safety incidents can have serious consequences. Prescriptive maintenance may offer better protection.
- Financial Resources: Predictive maintenance is more cost-effective upfront. Prescriptive maintenance costs more to set up but can deliver greater savings and reliability over time.
- Existing Infrastructure: If your systems already collect real-time data and perform predictive analysis, you may be closer to implementing prescriptive analytics.
- Long-Term Goals: Want to improve overall operational efficiency, reduce costs, and extend the life of critical assets? Prescriptive maintenance offers a competitive edge – if you’re ready for the complexity.
So, Which Strategy Is Best?
Choosing between predictive or prescriptive maintenance depends on your business’s size, goals, and current systems.
Predictive maintenance programs are easier to adopt, cost less, and still provide major benefits – especially in avoiding reactive maintenance and reducing equipment downtime. They’re ideal for companies that want a solid step up from traditional preventative maintenance.
Prescriptive maintenance systems go even further, offering deep insights and data-driven recommendations. They’re suited to businesses that have the resources and commitment to fully leverage advanced analytics and artificial intelligence.
No matter which path you take, moving away from reactive maintenance toward a proactive approach helps your team make more informed decisions, maintain optimal machine condition, and keep operations running smoothly.
- Predictive maintenance = uses real-time data and machine learning to predict failures.
- Prescriptive maintenance = uses AI to prescribe actions to prevent those failures.
- Predictive is cheaper and easier to implement.
- Prescriptive is more powerful but requires more data, infrastructure, and training.
- The right maintenance strategy depends on your industry, goals, and budget.
In the end, the best choice is the one that aligns with your business’s needs – and helps your maintenance teams stay ahead of potential failures before they become costly problems.