Business Challenge: Pioneering a Data-Driven Approach
Our client had already taken a step into the world of Machine Learning with a solution that utilized data dashboards for analysis. However, they needed more – a custom approach to efficiently collect, store, process, and analyze the massive amounts of data they were generating. Their goals included enhancing their predictive maintenance strategies, bolstering demand planning, and refining forecasting methods.
As their partner, we jumped into action, helping them transition from an out-of-the-box solution to a bespoke system that could handle extensive real-time data from various sensors. Together, we built a solution that spanned multiple operations, from optimizing production efficiency and forecasting machine reliability to planning maintenance and managing supply chain disruptions.
Our Collaborative Journey: Key Features and Solutions
To address the challenges faced by our client, we delivered an array of tailored services and solutions designed to meet their specific needs.
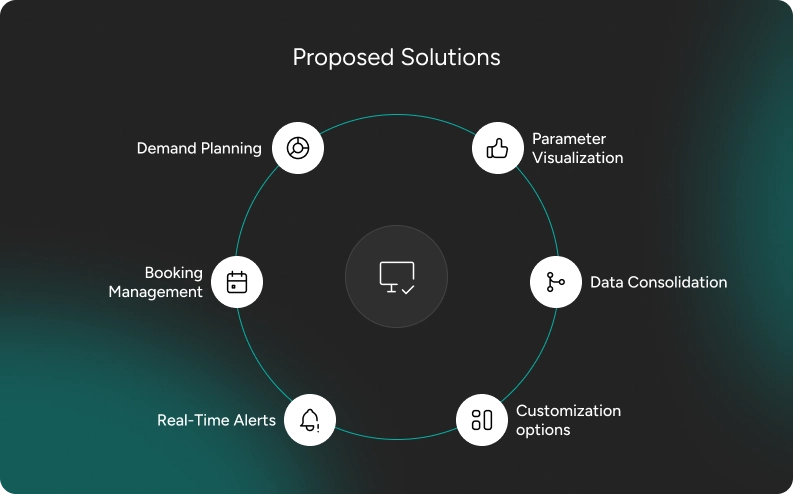
- Parameter Visualization: Our solution made it easy to access historical and real-time data for specific assets, uncovering relationships and predicting future values.
- Data Consolidation: By integrating data from various tools and systems into one robust application, we enabled engineers to work more efficiently and detect anomalies earlier. This involved pulling real-time data from an IoT Hub and processing it through EventHub into our custom system.
- Customization Options: Enhanced clarity and better decision-making processes were achieved through tailored features applicable across numerous operational areas.
- Real-Time Alerts: Our solution provided proactive maintenance alerts, helping prevent potential production breakdowns.
- Booking Management for Industrial Equipment: Efficiently managing equipment usage schedules, maintenance, and cleaning sessions was made possible.
- Demand Planning and Forecasting: This feature included management of mass energy and carbon emissions, aligning with sustainability goals.
- Cost Reduction: With a gradual digitization process and multi-year plan implementation, operational costs were significantly reduced.
The Benefits: Transforming Data into Actionable Insights
Our comprehensive service offering has significantly transformed our client’s operations. By leveraging our expertise, we helped turn their vast data into actionable insights. The outcome? Improved operational efficiency, minimized downtime, and smoother production processes.
Key features like real-time alerts, data consolidation, and parameter visualization enabled data-driven decision-making and a proactive maintenance approach. Our custom system's capacity to handle large volumes of data – hundreds of terabytes, in fact – illustrates its scalability and robustness. Just recently, tens of billions of records were generated from only two of their factories.
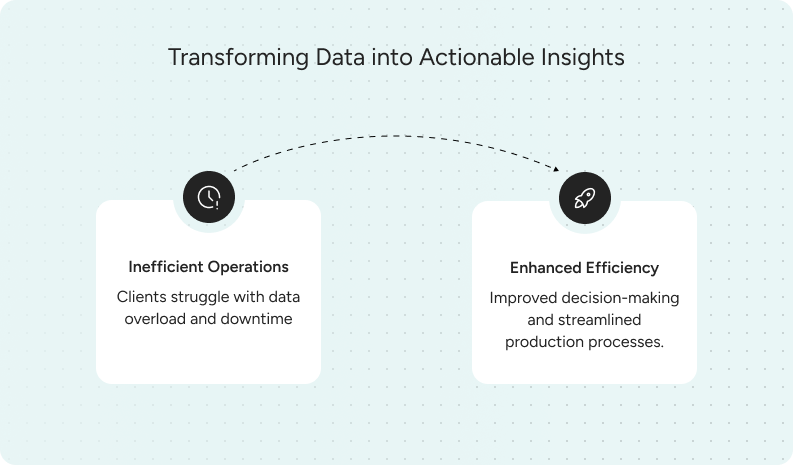
Transforming Data into Actionable Insights
See our case study to discover more details about this partnership.
A Predictive Future
Our collaborative efforts in predictive maintenance have provided essential domain knowledge and state-of-the-art Machine Learning solutions, helping our client scale their processes, transition to production, and enable live inference at operating sites. The implementation of AI solutions has significantly reduced real production costs by decreasing the frequency of maintenance periods.