Improving Reliability with Predictive Maintenance
Proactive approaches, like predictive maintenance, were designed to foresee potential equipment issues before they manifest into significant problems. By leveraging data and advanced technologies, predictive maintenance strategies offer a compelling way to improve reliability and efficiency.
Here’s a step-by-step guide to implementing these strategies in energy operations.
Step 1: Know Your Technologies
To implement predictive maintenance effectively, you need to integrate specific technologies that enable real-time monitoring and predictive analytics. Let’s dive in and learn more about the key technologies you should consider.
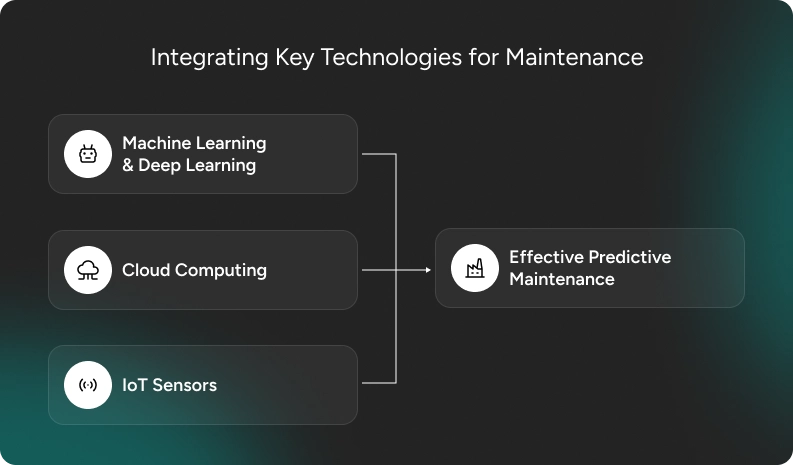
Analytics With Machine Learning & Deep Learning
Machine Learning (ML) and Deep Learning (DL) are indispensable for predictive maintenance. These algorithms analyze data collected from various sources to detect anomalies and predict equipment failure.
Depending on the nature and quality of the data, the team may decide to incorporate Supervised, Unsupervised, or a mixture of AI strategies. Unlike some other technologies, Machine Learning and Deep Learning are a must-have for predictive maintenance because they form the core analytical component that enables the prediction of future failures.
Using Cloud Computing for Data Processing
While Cloud computing alone does not equip you with predictive maintenance, it provides the necessary infrastructure for handling large volumes of data and performing complex analytics. Cloud platforms offer scalable storage and computational power, enabling the processing and analysis required for effective predictive maintenance.
By integrating these technologies, you create a robust system capable of real-time monitoring and predictive analytics, leading to more efficient and timely maintenance interventions.
IoT Sensors for Environmental Data
IoT sensors are also an essential factor for collecting real-time data. While modifying existing machinery to add sensors can be costly and complex, you can deploy IoT sensors to monitor environmental conditions such as humidity, temperature, and vibration around the machinery. This environmental data can be invaluable when combined with other data sources for predictive analytics.
Step 2: Define Objectives and Scope
Start by outlining clear objectives for your predictive maintenance (PdM) program. Ask yourself: What specific outcomes do you aim to achieve? Common goals include reducing downtime, extending equipment life, enhancing safety, and optimizing maintenance costs.
Define the scope of the program by identifying the equipment and processes that will be part of the initial deployment. A focused scope allows for a more manageable implementation and measurable results.
Step 3: Collect and Analyze Historical Data
Historical data is the foundation of any predictive maintenance strategy. Gather data from various sources, including equipment sensors, maintenance logs, operational records, and failure reports. This data will be instrumental in identifying patterns and trends that indicate potential failures. Employ data analytics tools to process and analyze the data, seeking insights into failure modes, rates, and contributing factors.
Step 4: Develop and Test Predictive Models
Develop predictive models tailored to your specific equipment and operations by using the data collected and integrated technologies. Start by creating initial prototypes with different Machine Learning and Deep Learning techniques to recognize early warning signs of potential failures. Train and validate these models on historical data to understand what constitutes normal and abnormal conditions.
Iteratively test and refine your models to enhance their accuracy and reliability. This trial-and-error process helps you find the most effective approach for your specific needs. Regularly update the models with new data to ensure they remain accurate and relevant. Through continuous improvement, these models will provide robust solutions for early detection of equipment failures, enhancing your maintenance strategies' efficiency and reliability.
You don't have to navigate this complex process alone! Our team of experts is available to assist you in developing, testing, and implementing predictive models tailored to your unique requirements, ensuring a smoother and more effective integration into your operations. See what we can do together.
Step 5: Implementation and Continuous Monitoring
With predictive models in place, implement the PdM strategy across your operations. Establish a system for equipment health monitoring, where data from IoT sensors is fed into the predictive models in real time. Create dashboards and alerts to ensure maintenance teams are promptly notified of potential issues.
Step 6: Measure Success Metrics
To determine the effectiveness of your predictive maintenance strategy, define key performance indicators such as:
- Reduction in Unplanned Downtime: Monitor the decrease in unplanned downtime incidents.
- Maintenance Cost Savings: Calculate cost savings from reduced emergency repairs and extended equipment life.
- Reliability Improvement: Assess improvements in equipment reliability and overall operational efficiency.
Regularly review these metrics to refine and enhance your PdM strategy.
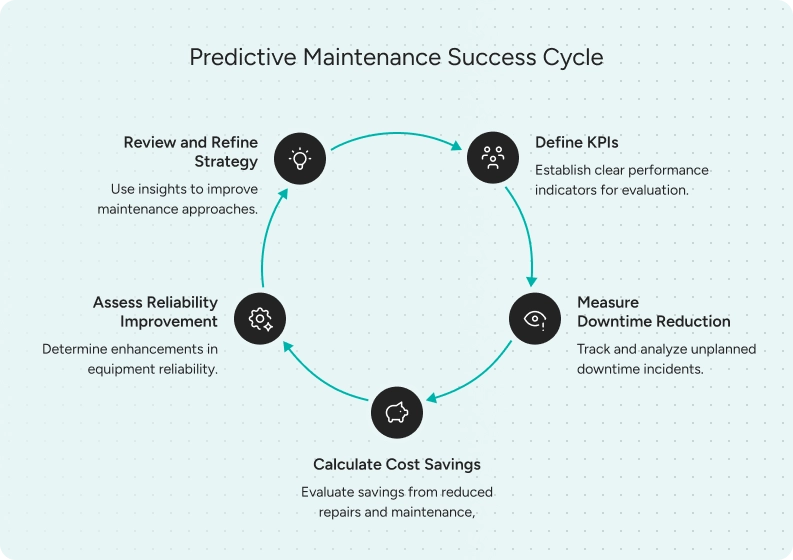
Achieving Sustainable Efficiency
Implementing predictive maintenance in the energy sector (or any other industry) is a transformative step toward operational excellence. By anticipating issues before they arise, you can significantly reduce downtime, improve safety, and achieve substantial cost savings. The journey to predictive maintenance requires careful planning, the right technology, and continuous monitoring. However, the benefits far outweigh the initial investment.